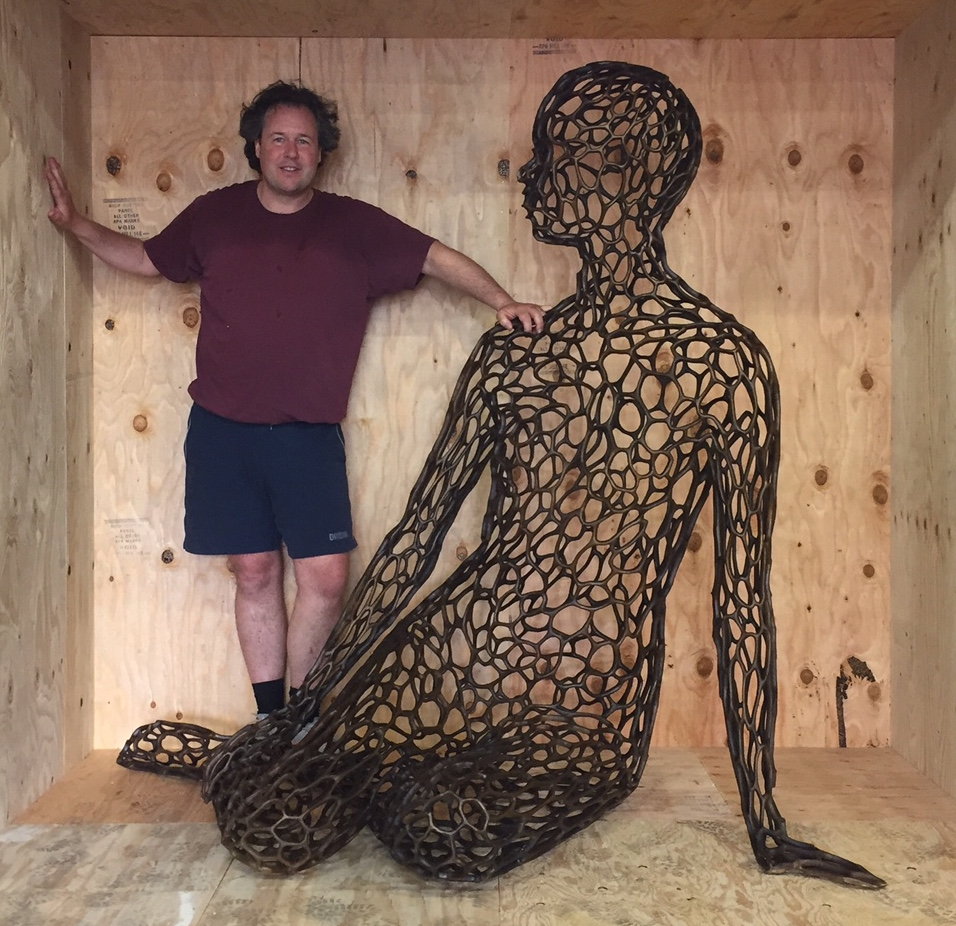
With a cluster of eight LulzBot TAZ 3D Printers and a passion for art, sculptor Julian Voss-Andreae is embracing 3D printing as an affordable way to help create monumental sculptures. His work has garnered worldwide attention, being featured in various broadcast and print media ranging from Oregon Public Broadcasting Television to Sculptural Pursuit magazine.
“3D printing and subsequent direct casting allows me to create sculptures of essentially arbitrary design for a price that is comparable with traditional hand sculpting methods,” Voss-Andreae said.
One of Voss-Andreae’s recent projects is a large-scale sitting female figure to be installed outside Georgia Tech’s new Engineered Biosystems Building (EBB). This particular sculpture, which features a Voronoi-inspired open lattice design to accommodate plant growth on the ground, will soon be unveiled and bring a sense of whimsy to the site while visually and conceptually tying in with the building’s fields of research.
Voss-Andreae’s Georgia Tech sculpture is made from cast bronze, a metal that ages gracefully, allows rich patination, and has low maintenance requirements. However, the time-intensive process used to create it started with more than 100 large components 3D printed in PLA, amounting to around 10,000 hours of print time on Voss-Andreae’s LulzBot 3D Printers.
After 3D printing, Voss-Andreae’s process looks much like typical investment casting. The pieces are coated with a sealant to smooth the surface finish, and then prepared for casting with repeated dipping in a ceramic slurry. Once the ceramic shell is appropriately thick, the PLA pattern is burned out in a kiln, leaving a perfect negative mold that the molten bronze is poured into. After cooling, the mold is broken away, and the bronze parts are sandblasted to leave a clean and uniform finish. Then, the parts are assembled and welded together one by one, a huge and complicated 3D puzzle. Finally, the welds are tooled out to ensure everything is smooth and ready for the patina.
[Watch a tour of Voss-Andreae's workspace.]
Voss-Andreae’s large-format LulzBot TAZ 3D Printers also serve purposes beyond the casting process.
“They build useful parts, including parts used to upgrade them,” Voss-Andreae said. “They also print maquettes and parts of sculptures we are working on to plan the fabrication process and to aid in visualizing the end product.”
The long-term reliability and Open Source Hardware design of LulzBot 3D Printers helped guide Voss-Andreae’s purchasing decision and allowed for subsequent upgrades and modifications to be made.
“The quality is pretty much as good as it gets,” Voss-Andreae said.
As a sculptor looking for ways to streamline the creative process, Voss-Andreae finds LulzBot 3D Printers valuable to his workflow.
“The main benefit to me is that I am now able to create life-size bronze sculptures for a price that allows experimentation,” Voss-Andreae said.
Explore More Creative Applications with LulzBot 3D Printers ➡
Photos licensed CC BY-SA 4.0 International © Julian Voss-Andreae.