Footwear Maintenance and Repair
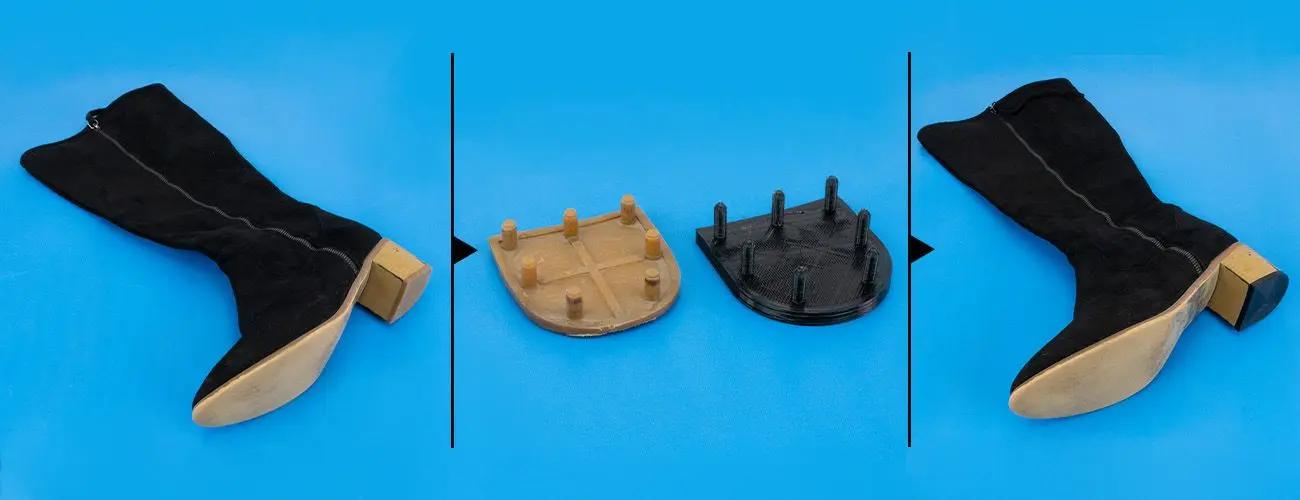
Have you ever had to throw out a pair of otherwise good footwear because of a damaged or worn out heel? With 3D printing, you can extend the life of your favorite boots with some reverse engineering and adhesive.
What You'll Need:
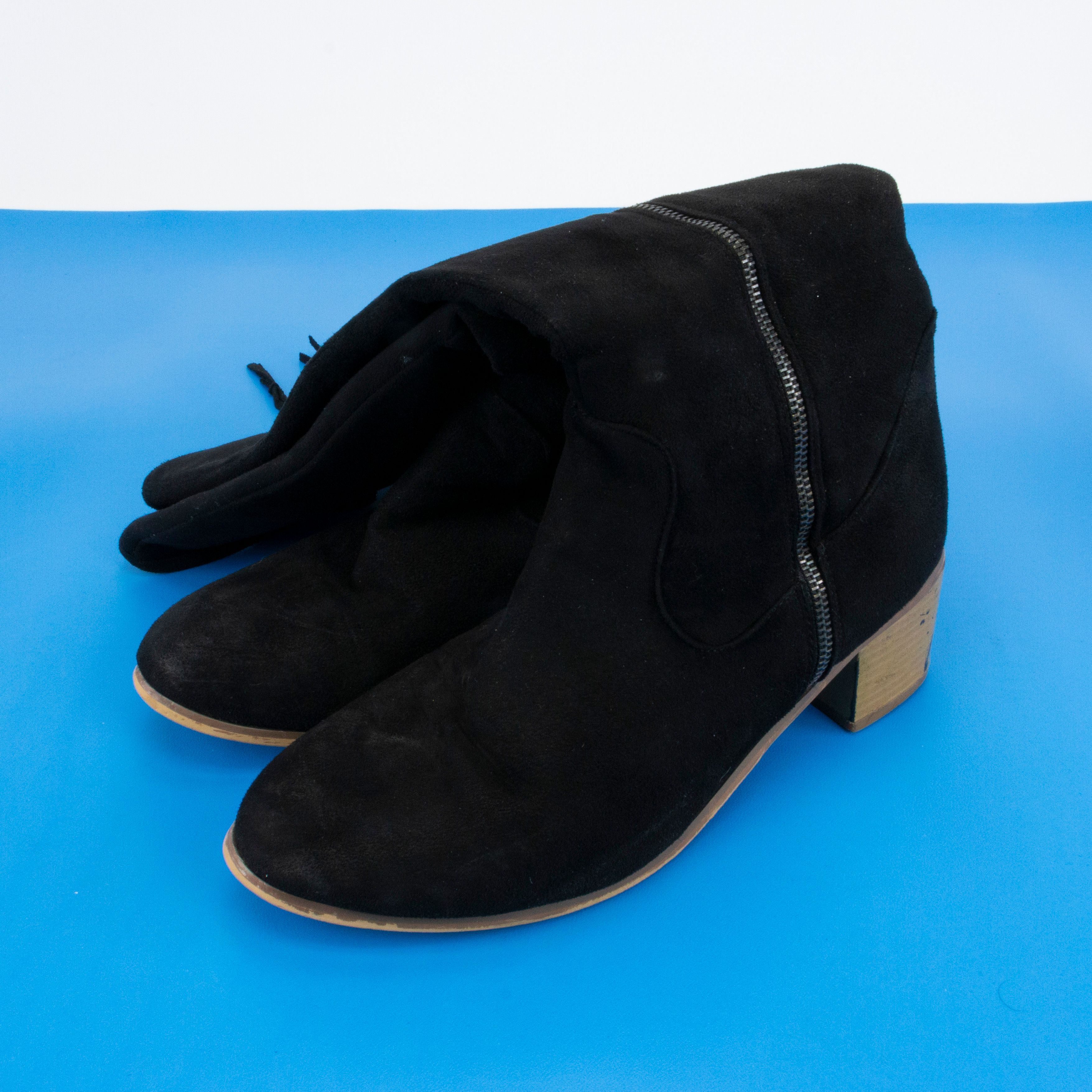
- Used Footwear
- Putty Knife
- LulzBot Printer
- TPU such as NinjaFlex, PolyFlex, or other flexible material
- Digital Caliper
- Pen and Paper
- 2 Part Epoxy
- Wood Clamps
- Small Board
Instructions:
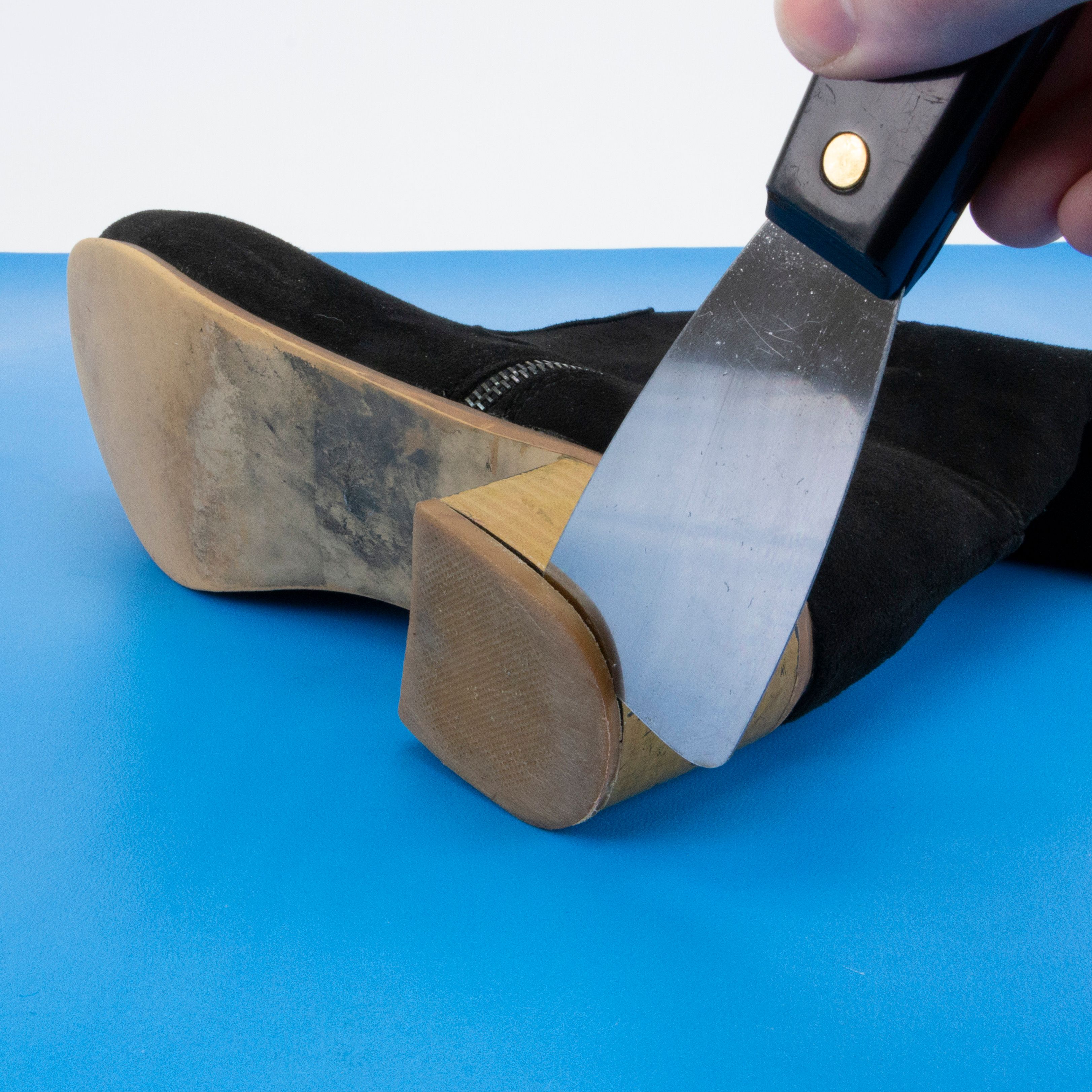
Step 1:
First, gather your materials and remove the damaged heel from your footwear. We carefully used a putty knife to avoid damaging the rest of the boot and the pegs holding in the heel. Please note that not every piece of footwear will be a good candidate for this process. If you are planning to throw the footwear out anyway, it's worth trying!
Step 2:
Once the heel is removed, we can get to work on reverse engineering a replacement part. Other than the curved portion, this is a very simple design which can be created by extruding basic shapes. Use the digital caliper to get the dimensions of the part, keeping notes and drawing the basic design on paper. Make sure to get the depths/heights and try to make center points for the pegs. *You can also take a photo of the part next to a ruler or scan a traced outline of the part you don't have a caliper.
There are several options for software, which are either open source or free for non-commercial purposes. This Community Page has a list of popular 3D modeling software to choose from. A nice software for a new designer is TinkerCAD. If your looking for a software that you can grow into, it may be worth your time to learn Fusion 360.
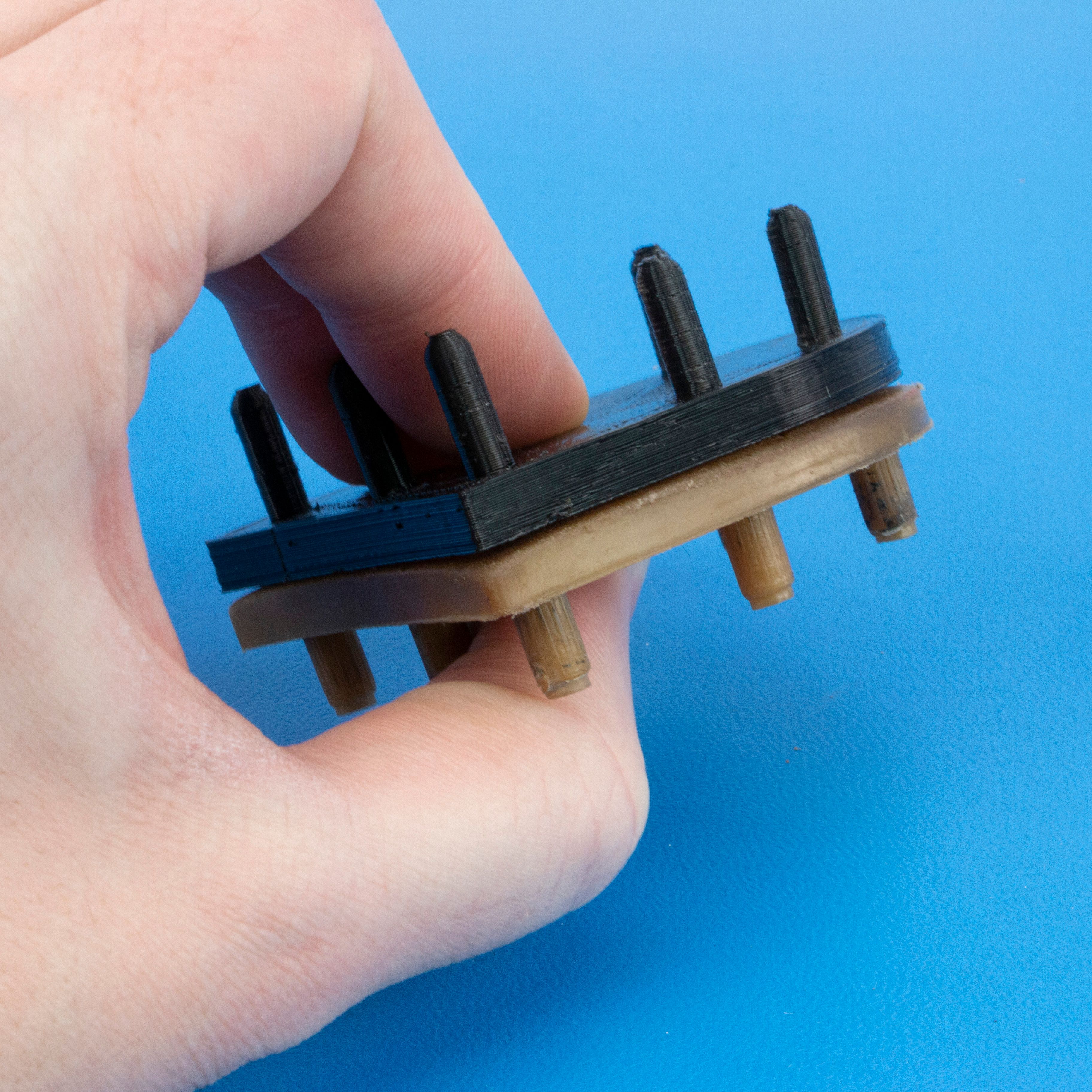
Step 3:
After the part is designed and you've exported an STL file, you can start printing! We printed with NinjaFlex, a flexible material made of TPU which has more grip and better shock absorption that other materials. It printed well on our Mini 2 but will work with any LulzBot machine equipped with a modern Tool Head (SE, HE, M175 v2, H175, etc). Make sure to use the NinjaFlex material reset in Cura LE and glue stick on your print surface.
Design tip: Since this will be a part which will encounter a lot of abrasion, you will want to have a high infill and shell count. 50% infill and 5+ shells would be a good start.
- You will likely need to do a few iterations of your design. If you don't have a lot of material for test prints, you can print just a portion by splitting it either in your design software or Meshmixer.
You can also sink prints into the bed in Cura LE and only parts above 0mm in the Z axis will print.
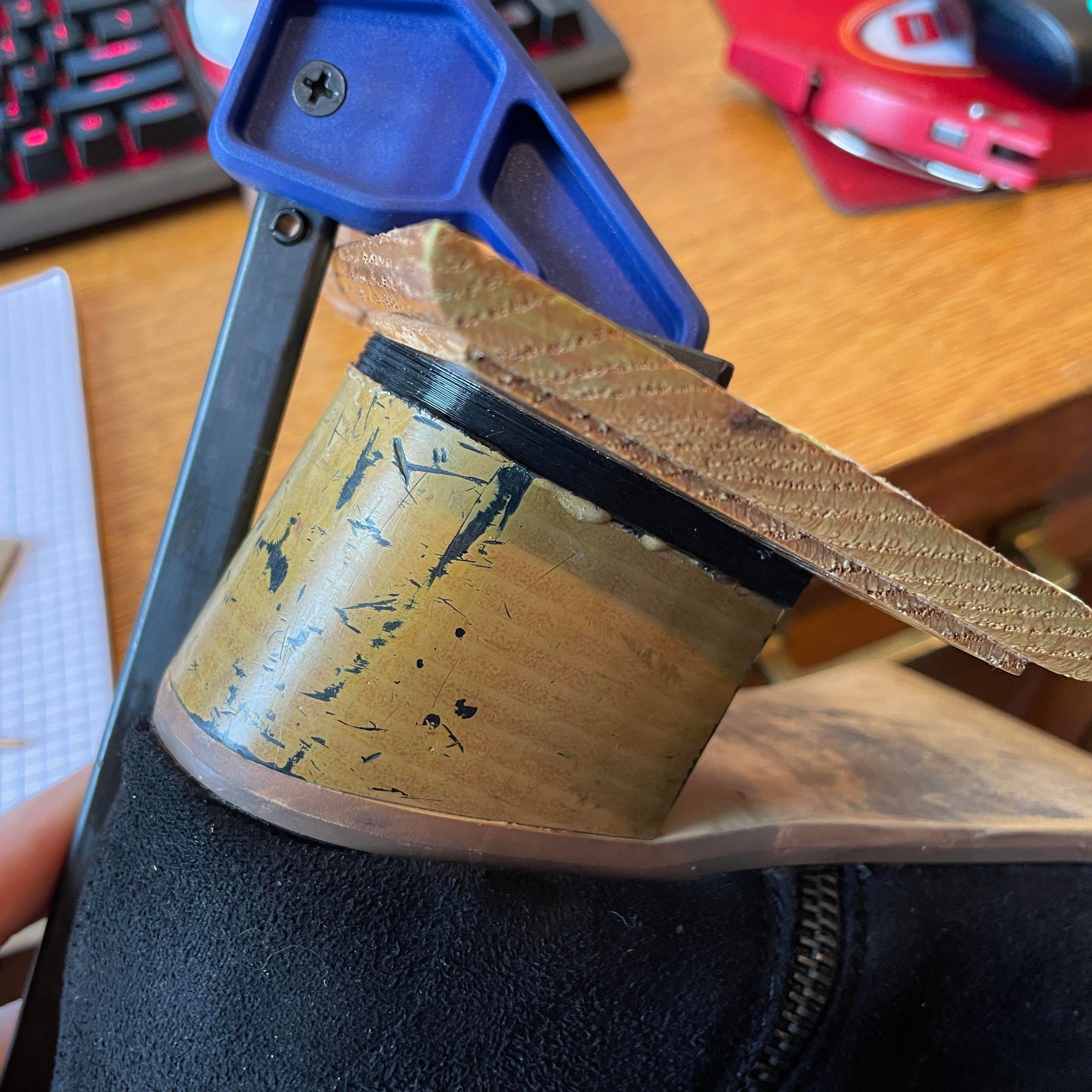
Step 4:
Grab the clamp and small board. The idea is to create a larger surface area to allow for even pressure on the heel. The force should be perpendicular to the flat surface. Allow the part to sit for the time recommended by your adhesive's instructions.
Step 5:
After drying, check your results and ensure that the heel is securely attached. If there is excess adhesive after clamping, remove it with sandpaper or a razor.
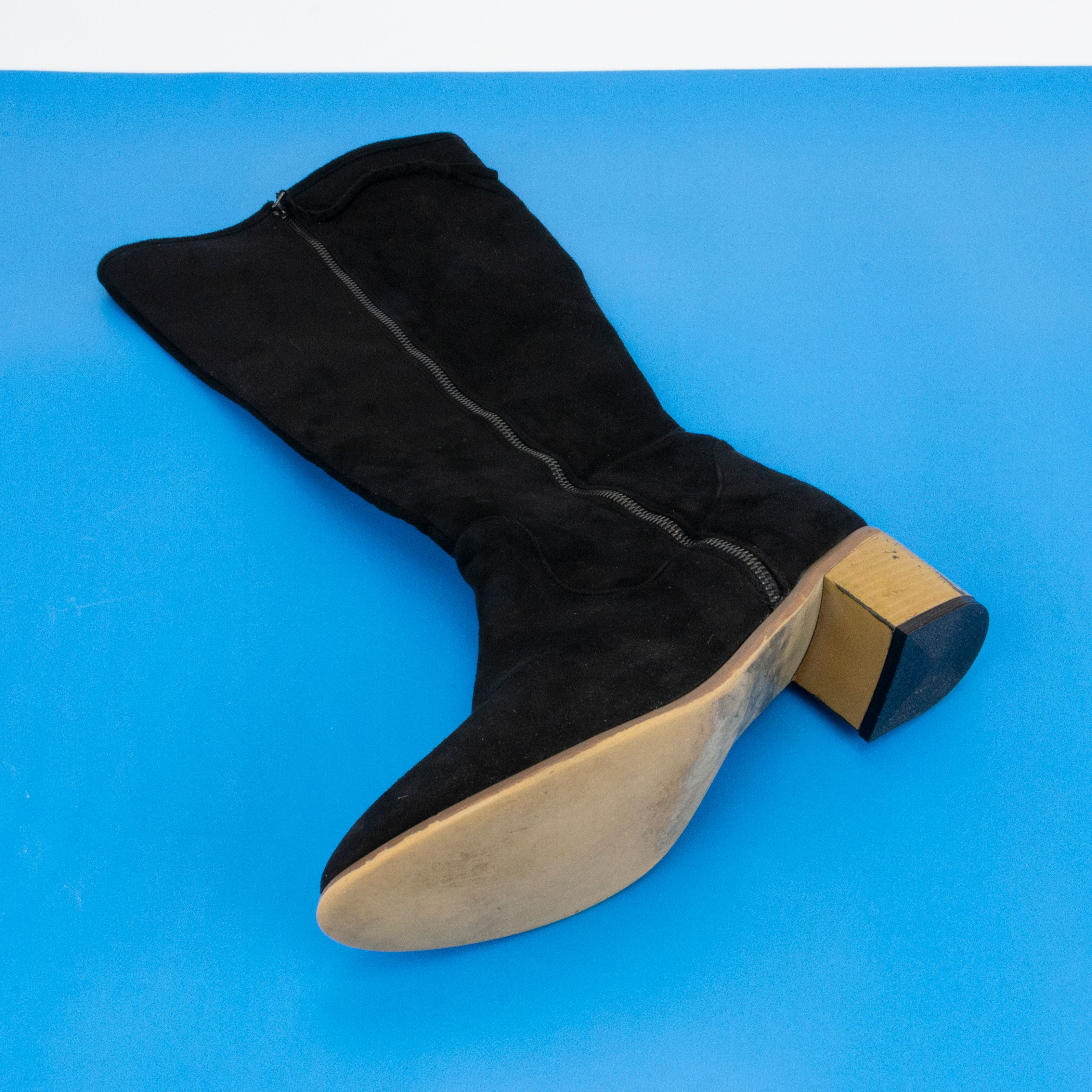
Step 6:
Congratulations, you've brought life back into your footwear! This idea can be transferred to many household items for simple fixes. The printed part may not last as long as the original depending on the material, so you may want to print a few extras. In the case that the heel's design isn't symmetrical, you can mirror the design in Cura LE with the "Mirror" function for the other boot.